KROS Otomotiv operates a state-of-the-art manufacturing facility, in which we continuously invest to meet the ever-increasing demands of the automotive industry. Our production processes and procedures are constantly updated, expanded, and improved through innovative approaches.
Our main production processes include:
RUBBER EXTRUSION AND FORMING: Using state-of-the-art extrusion lines and automation, we produce single or multi-ply rubber hoses, both braided and non-braided. These hoses are shaped according to various geometric structures and undergo vulcanization in autoclaves with process automation.
POLYAMIDE EXTRUSION AND FORMING: Our extrusion lines, guided by automatic control systems, produce flat or formed, hard or soft polyamide pipes used in various fluid transfer systems in automobiles. Special molding methods are employed to shape these pipes.
METAL PIPE FORMING: Steel and aluminum pipes of different sizes are shaped using fully and semi-automatic bending machines. Spot welding, gas welding, and brazing processes are carried out in our high-tech machine park.
ASSEMBLY: Rubber hoses, polyamide pipes, and steel pipes produced by KROS Automotive are assembled together with other purchased parts for fluid transmission in vehicles. The assembled products undergo rigorous testing on specialized tables equipped with digital cameras to ensure leak tightness and proper flow control.
For products that require special cleaning criteria due to their function in the vehicle, assembly and testing processes are conducted in a dedicated production environment isolated from other processes. This controlled environment maintains constant monitoring of airborne particle levels, temperature, humidity, and pressure. Additionally, an electrostatic discharge (ESD) feature is implemented to prevent damage to materials sensitive to electrostatic charges.
POLYURETHANE COATING: We apply a specialized high-tech polyurethane coating with unique geometries defined by customer drawings. This coating is lightweight yet covers a large surface area, meeting the specific requirements outlined by our customers.
At KROS Automotive, we prioritize quality and precision throughout our production processes to deliver reliable automotive components that meet the highest industry standards.
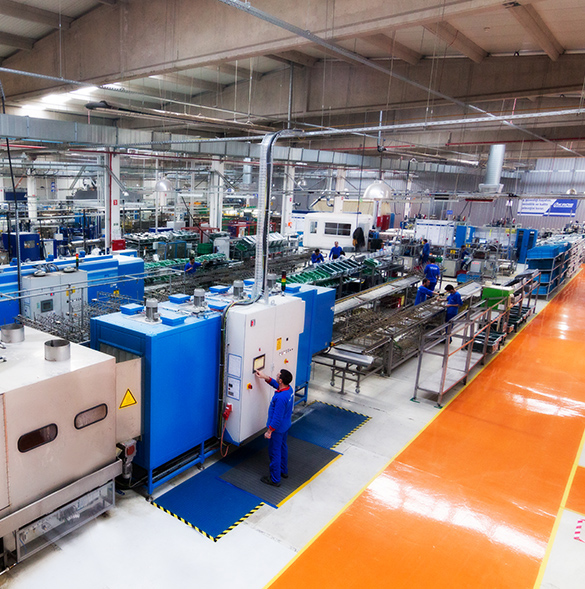